Operations Talent: Shane
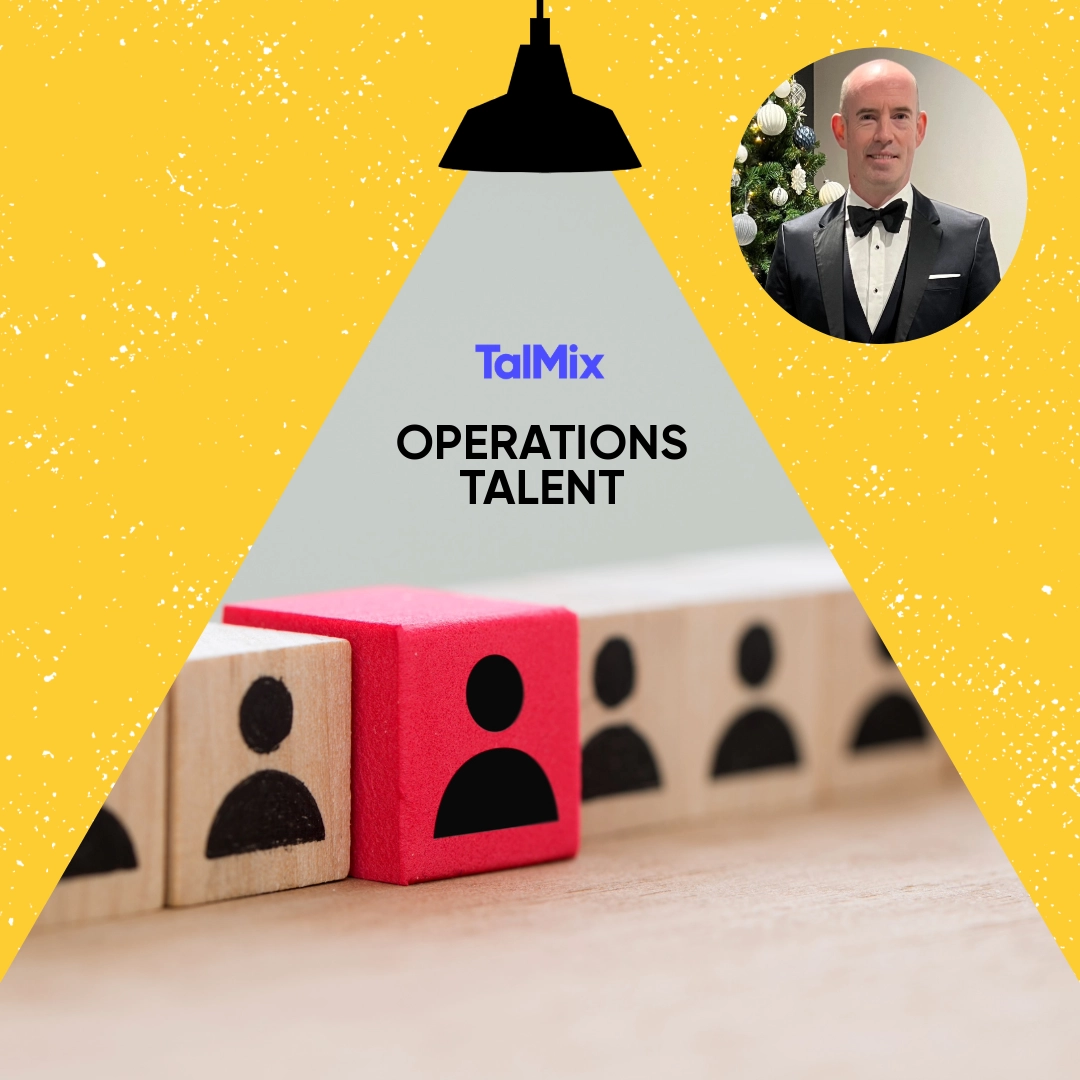
Shane is a vastly experienced manufacturing consultant and professional chartered engineer (experienced in lean manufacturing methods), driving change that leads to increased productivity and reduced costs. His core specialities include Advanced Quality Techniques, Lean Manufacturing, Manufacturing Engineering and Change Management.
Q. When you’re at a networking event, how do you describe your independent career status, and where you focus your work?
I focus on providing interim management solutions or provision of specialist skills for OEM/Tier 1 businesses operating in manufacturing environments. Ad-hoc short-term assignments are also taken providing specialist support across Quality, Lean, Project Management and Manufacturing Engineering.I have many years of experience across the aerospace, automotive, defence, naval nuclear, ultra-high vacuum and precision machining sectors, having held senior engineering, managerial and consultant roles working with clients across the UK, Europe and the USA.
Specialising in:
- Leadership Coaching and Change Management
- Site Relocation Projects
- Advanced Quality Techniques (FMEA, SPC, MSA, 6 Sigma, 8D, A3)
- Lean Manufacturing (5S Workplace Organisation, 7 Wastes, Process Flow Analysis, Gemba Kanri, Policy Deployment, Line Balancing, Standardised Work)
- Quality Systems (ISO9000, IATF16949, EN9100)
- Business Specific Systems (Ford/Toyota Production System, Rolls-Royce SABRe, Airbus IPCA+)
- Expert Witness Reports for Industrial Court Cases
-
Q. What are the specific benefits that you, as an independent, offer to the operating teams/portfolio company leadership? How do you explain the value your expertise brings and the specific situations in which you should be engaged?
I engage with a clients team to challenge the status quo and identify opportunities to improve utilising available data. Having worked across multiple manufacturing sectors I understand one size doesn't fit all and often solutions must be tailored to the business and its people. Making timely and data-driven decisions is key to progressing at pace.
As a Leadership Coach I believe the people who do the work know the answers to their problems, typically lack of engagement and/or empowerment prevents them from taking action. Involving and engaging the people by 'bringing them with you' is the only way to implementing sustainable improvement and realising the benefits. I thrive on engaging with new teams and watching them grow on their own personal journey of improving their place of work. Going to where the work is done and listening to those people who do the work is the best way to understand the way forward.
As a natural problem solver I'm comfortable in most manufacturing sectors, although my core experience is Automotive, Aerospace, Naval Nuclear, Survival and Defence. My areas of expertise are Quality, Lean (OpEx), Project Management and Manufacturing Engineering.
Q. Why do you think there is increasing demand for independent expertise with PE operating teams?
When a PE operating team acquires a new business they may not have experience of that particular sector. Choosing to seek independent expertise is a great way to quickly understand what improvement opportunities are available and how these can positively impact the profitability of a business.
Q. Describe a recent or successful assignment in terms of scope, duration and any particular highlights in the outcomes.
My largest (and most significant) assignment for a client was a site move including full re-qualification to produce from a new location. Essentially the project was to relocate a number of satellite facilities into one larger unit with minimal disruption to the current customer order book. Most significant achievement was a 40% cost saving on the original surveyors quote for M&E installation works. This project lasted 2 years from initial rip out of the brownfield location up to re-qualification to produce in a new site.
The highlights are below:
- Contracted to project manage a site expansion plan, moving from 7 units (4 joined, 2 joined and 1 since unit) circa 45,000 sqft. total on opposite sides of a small industrial estate road into one brownfield location of approx 61,000 sqft.
- Involved overseeing Landlord rip-out and office refurb activity, unit was previously a cold store warehouse and packing logistics warehouse.
- Analyse current and forward order book to determine main products and or product groups (runners, repeaters, strangers analysis) with opportunity for designated cell manufacture (to implement flow) with multiple machine types in each cell.
- Develop factory flow for all processes to minimise distance travelled between processes.
- Develop QA and Laboratory areas layouts.
- Coordinate Mechanical & Electrical factory design to provide all services with Principal Designer, including power, compressed air, chilled water (as required) and data to every machine.
- Run tender event for M&E works in conjunction with Group Procurement.
- Down select potential suppliers and Value Engineer works with chosen supplier to reduce installation costs (eventually saving £1.2m on initial Surveyor quoted works - £2.9m down to £1.7m).
- Oversee M&E fit-out with Principal Contractor.
- Coordinate off-book works with specialist suppliers not under Principal Contractor (Recommissioning of specialist equipment.
- Vacuum and Oil Quench Furnaces).Instigate and oversee all machine moves and recommissioning activity for standard equipment (CNC and manual machines).
- Liaise with all customers over transfer of works plan.
- Coordinate all qualification and re-approval works (I have been this sites Interim Quality Manager previously) for customers and regulatory bodies (AS9100 and 5 NADCAP approvals).
- Complete all of the above with minimal disruption to customer supply whilst building buffer stocks to bridge gap between moving machines and prequalifying new location.
Q. What advice would you give to anyone about to embark on an independent career as to how they can provide the best results for a client, while fulfilling their own career path?
My best advice to anyone looking to start up on their own, is that whilst looking after the client is an absolute priority, remember to take good care of yourself! It's easy to throw yourself into working every hour you can when you first start up (I did!), but that can quickly lead to burning yourself out; and you're no use to your client or yourself when you hit the wall.It's easy to say with experience... but take time for yourself, learn to switch off at the end of the day and have an outlet that helps you de-stress.
I always take lunch away from my desk during the week. That 30 minutes away from it all halfway through the day, helps you re-energise for the second half. When I'm off the clock, I'm off the clock! Emails can wait until the morning; I'd take an urgent call - emails are not urgent. Don't spend your evening trawling through them. Finally, have an energetic outlet, I throw some weights around the gym (not literally), but it could be going for a run, bike ride, swim, martial arts, gym class... you name it - go and do it. Releasing some endorphins after a day's work can really help you relax in the evening and reset for the next day.
Q. What's your favourite thing to do when you're not on the clock?
I like to watch films, play music (or mix on my decks - used to DJ at University) and I'm a collector of Lego, records, films, hardback comic novels and Nerf guns! I also spend time in the gym strength training and I'm learning to ice skate with my daughter.
Looking for Lean (OpEx), Quality & Engineering Specialists? Engage with talent like Shane by posting a project now, or by talking to us about how to build up a pool of similar talent in the field.